Solder Ball Attach – Process Engineer
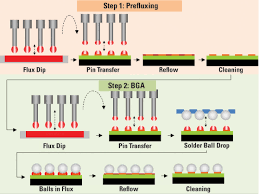
In the realm of electronics manufacturing, where miniature components and intricate circuitry converge, the role of a process engineer holds paramount importance. Among the myriad processes involved, solder ball attach stands out as a critical stage, especially in the assembly of semiconductor devices. This article delves into the intricacies of solder ball attach and elucidates the indispensable contributions of a process engineer in ensuring its efficacy and reliability.
Understanding Solder Ball Attach
Solder ball attach, also known as ball grid array (BGA) assembly, is a pivotal step in semiconductor packaging. BGAs are a type of surface-mount packaging used for integrated circuits, facilitating the interconnection between the chip and the printed circuit board (PCB). The process involves attaching solder balls to the underside of the semiconductor device, which are then aligned with corresponding pads on the PCB for soldering.
The solder balls, typically made of a tin-lead alloy or lead-free compositions such as SAC (tin-silver-copper), undergo precise placement and reflow soldering to establish electrical and mechanical connections. This method offers numerous advantages over traditional packaging techniques, including enhanced thermal and electrical performance, reduced footprint, and improved reliability.
Challenges in Solder Ball Attach
Despite its advantages, solder ball attach presents several challenges that necessitate meticulous attention to detail. These challenges include:
- Solder Ball Uniformity: Achieving uniform size, shape, and alignment of solder balls is crucial for ensuring consistent electrical connections and minimizing defects such as bridging or open circuits.
- Thermal Management: Effective thermal management is essential to prevent solder ball deformities or solder joint cracking during reflow soldering, which can compromise the integrity of the assembly.
- Process Control: Maintaining precise control over parameters such as temperature profiles, solder paste deposition, and placement accuracy is imperative to mitigate defects and ensure high yield rates.
- Reliability Concerns: The reliability of solder joints is paramount, particularly in applications subjected to mechanical stress or thermal cycling. Factors such as material selection, solder alloy composition, and assembly design play a crucial role in determining long-term reliability.
Addressing these challenges requires a comprehensive understanding of materials science, soldering techniques, and manufacturing processes, underscoring the indispensable role of a process engineer in solder ball attach.
The Role of a Process Engineer
A process engineer serves as a linchpin in the solder ball attach process, orchestrating various aspects to optimize performance, yield, and reliability. Their responsibilities encompass:
- Process Development: Process engineers are tasked with developing and refining solder ball attach processes to meet stringent quality standards and performance requirements. This involves conducting feasibility studies, designing experiments, and optimizing process parameters to enhance efficiency and yield.
- Materials Selection: Selecting appropriate solder alloys, fluxes, and substrate materials is critical for achieving robust solder joints with the desired mechanical and electrical properties. Process engineers evaluate material compatibility, reliability data, and regulatory compliance to make informed decisions.
- Equipment Optimization: Process engineers work closely with equipment vendors to optimize solder ball attach machinery, ensuring precise control over deposition, placement, and reflow processes. They oversee equipment calibration, maintenance, and troubleshooting to minimize downtime and maximize throughput.
- Quality Assurance: Quality assurance is a cornerstone of solder ball attach, and process engineers play a pivotal role in implementing rigorous inspection and testing protocols. They utilize advanced inspection techniques such as X-ray imaging, optical microscopy, and automated optical inspection (AOI) to detect defects and deviations from specifications.
- Continuous Improvement: Process engineers are committed to continuous improvement, leveraging data analytics, statistical process control (SPC), and feedback mechanisms to identify opportunities for enhancement. By analyzing process performance metrics and customer feedback, they drive iterative improvements to optimize yield, cost, and cycle time.
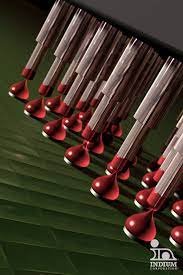
Conclusion
In the intricate tapestry of electronics manufacturing, solder ball attach emerges as a pivotal process, underpinning the functionality and reliability of semiconductor devices. The role of a process engineer in solder ball attach cannot be overstated, as they navigate complex challenges to ensure optimal performance, yield, and reliability. Through meticulous process development, materials selection, equipment optimization, quality assurance, and continuous improvement initiatives, process engineers uphold the highest standards of excellence in semiconductor packaging. As technology advances and demands for miniaturization and performance escalate, the expertise and ingenuity of process engineers will remain indispensable in shaping the future of electronics manufacturing.