Quality Engineer
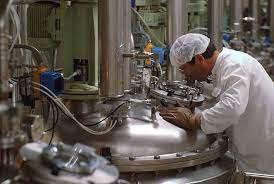
Introduction: In today’s fast-paced and highly competitive business landscape, quality has become a cornerstone of success. Whether it’s manufacturing, software development, healthcare, or any other industry, maintaining high standards of quality is paramount. This is where quality engineers play a pivotal role. They are the unsung heroes behind the scenes, ensuring that products and services meet or exceed customer expectations. In this article, we delve into the multifaceted responsibilities of quality engineers and why their role is indispensable in modern-day industries.
Defining the Role of a Quality Engineer: Quality engineers are professionals tasked with ensuring that products or services meet specified quality standards. They work across various industries, from manufacturing and construction to software development and healthcare. The primary objective of a quality engineer is to identify defects, improve processes, and enhance overall product quality. They employ a range of techniques, tools, and methodologies to achieve these goals, including statistical analysis, quality control, and continuous improvement initiatives.
Responsibilities of a Quality Engineer: The responsibilities of a quality engineer can vary depending on the industry and the specific needs of the organization. However, some common tasks and duties include:
- Quality Assurance: Quality engineers are responsible for developing and implementing quality assurance processes to ensure that products or services meet established standards. This may involve creating quality control plans, conducting audits, and performing inspections to identify any deviations from the desired quality levels.
- Defect Analysis: When defects or non-conformances occur, quality engineers are tasked with identifying the root causes and implementing corrective actions to prevent recurrence. They use various problem-solving techniques such as root cause analysis, fishbone diagrams, and 5 Whys to determine the underlying issues and develop effective solutions.
- Process Improvement: Continuous improvement is a core principle of quality engineering. Quality engineers actively seek opportunities to optimize processes, reduce waste, and enhance efficiency. They may use methodologies like Six Sigma, Lean Manufacturing, or Total Quality Management to streamline operations and drive performance improvements.
- Supplier Quality Management: In industries reliant on external suppliers, quality engineers play a crucial role in evaluating supplier performance and ensuring that purchased materials and components meet quality requirements. They may conduct supplier audits, establish quality agreements, and provide guidance on supplier development initiatives.
- Regulatory Compliance: Many industries are subject to stringent regulatory requirements and quality standards. Quality engineers are responsible for ensuring that products and processes comply with relevant regulations and certifications, such as ISO 9001, FDA regulations, or industry-specific standards.
- Data Analysis: Quality engineers rely on data analysis techniques to monitor performance, identify trends, and make data-driven decisions. They use statistical tools and software to analyze quality metrics, defect rates, and process capabilities, enabling them to identify areas for improvement and measure the effectiveness of quality initiatives.
- Training and Education: Quality engineers often provide training and guidance to employees on quality-related topics, including quality standards, best practices, and quality management systems. They may develop training materials, conduct workshops, and mentor team members to ensure a culture of quality excellence within the organization.
Importance of Quality Engineers: The role of quality engineers is indispensable for several reasons:
- Customer Satisfaction: By ensuring that products and services meet or exceed customer expectations, quality engineers contribute to customer satisfaction and loyalty. High-quality products not only meet functional requirements but also deliver superior performance, reliability, and durability, enhancing the overall customer experience.
- Cost Savings: Quality issues can be costly for organizations, leading to scrap, rework, warranty claims, and potential recalls. Quality engineers help minimize these costs by preventing defects, improving processes, and optimizing resource utilization. By identifying and addressing quality problems early in the production process, they help avoid costly rework and ensure efficient use of resources.
- Brand Reputation: In today’s interconnected world, a company’s reputation can make or break its success. Quality engineers play a vital role in safeguarding the brand reputation by ensuring consistent quality across products and services. A reputation for high quality can differentiate a company from its competitors and build trust and credibility among customers and stakeholders.
- Regulatory Compliance: Non-compliance with regulatory requirements can have severe consequences for businesses, including fines, legal penalties, and damage to reputation. Quality engineers help organizations navigate complex regulatory landscapes by ensuring that products and processes adhere to applicable standards and regulations. By staying abreast of regulatory changes and proactively addressing compliance issues, they mitigate risks and ensure business continuity.
- Continuous Improvement: Quality engineers drive a culture of continuous improvement within organizations, encouraging innovation, efficiency, and excellence. By identifying opportunities for optimization and implementing best practices, they help organizations stay competitive in dynamic markets and adapt to changing customer needs and market trends.
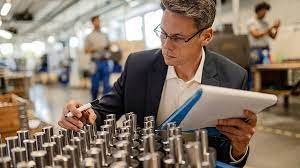
Conclusion: Quality engineers play a critical role in ensuring that products and services meet or exceed quality standards, thereby contributing to customer satisfaction, cost savings, brand reputation, regulatory compliance, and continuous improvement. Their multifaceted responsibilities encompass quality assurance, defect analysis, process improvement, supplier quality management, regulatory compliance, data analysis, and training. In today’s competitive business landscape, organizations that prioritize quality engineering are better positioned to succeed and thrive in the long term.