Welding Operator Electronics
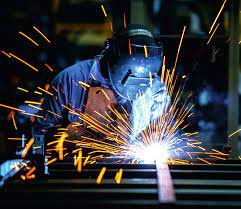
Introduction: Welding, an essential process in various industries, has witnessed significant technological advancements over the years. One of the key areas of innovation lies in welding operator electronics, where sophisticated electronic systems are integrated into welding machines to enhance precision, efficiency, and safety. This article delves into the evolution of welding operator electronics, highlighting its importance, applications, and future prospects.
Evolution of Welding Operator Electronics: Traditional welding processes relied heavily on manual techniques, where operators had to rely on their skills and experience to achieve desired results. However, with the advent of electronics, welding machines have undergone a transformation, enabling operators to perform tasks with unprecedented accuracy and consistency.
The early iterations of welding operator electronics primarily focused on automating certain aspects of the welding process, such as regulating voltage, current, and wire feed speed. These rudimentary electronic systems paved the way for more sophisticated technologies, including microprocessors, sensors, and advanced control algorithms.
Modern Welding Operator Electronics: Today, welding machines are equipped with a myriad of electronic components and features that empower operators to achieve superior weld quality and efficiency. Some of the key advancements in modern welding operator electronics include:
- Digital Control Systems: Welding machines now feature digital control systems that offer precise control over welding parameters such as voltage, current, and wire feed speed. These systems allow operators to fine-tune settings with greater accuracy, resulting in consistent welds and reduced rework.
- Adaptive Welding Technologies: Adaptive welding technologies utilize sensors and real-time feedback mechanisms to adjust welding parameters in response to changing conditions. For example, adaptive control systems can automatically compensate for variations in material thickness, joint fit-up, and electrode wear, ensuring optimal weld quality throughout the process.
- Welding Process Monitoring: Electronic systems integrated into welding machines enable real-time monitoring of key process variables, such as arc voltage, arc current, and wire feed speed. By continuously analyzing this data, operators can detect anomalies and make adjustments to prevent defects before they occur.
- Remote Control and Monitoring: Many modern welding machines feature remote control capabilities, allowing operators to adjust settings and monitor welding parameters from a distance. This functionality enhances safety by reducing the need for operators to be in close proximity to hazardous welding environments.
- Integrated Welding Management Systems: Welding operator electronics are increasingly being integrated into broader welding management systems that provide comprehensive oversight of welding operations. These systems can track weld parameters, manage welding procedures, and generate detailed reports for quality assurance purposes.
Applications of Welding Operator Electronics: The advancements in welding operator electronics have found applications across a wide range of industries, including:
- Automotive Manufacturing: In the automotive industry, welding operator electronics are used extensively for robotic welding applications, where precision and consistency are critical for producing high-quality welds in vehicle components.
- Aerospace Fabrication: Aerospace manufacturers rely on welding operator electronics to meet stringent quality standards for welding aircraft structures and components. The ability to precisely control welding parameters ensures the integrity and reliability of critical aerospace assemblies.
- Construction and Infrastructure: In the construction sector, welding operator electronics play a vital role in fabricating structural steel components for buildings, bridges, and other infrastructure projects. These technologies enable welders to achieve strong and durable welds that meet regulatory requirements.
- Energy Sector: Welding operator electronics are essential for fabricating pipelines, pressure vessels, and other equipment used in the energy sector, including oil and gas exploration, power generation, and renewable energy projects. The ability to monitor and control welding processes ensures the safety and integrity of energy infrastructure.
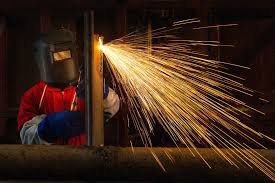
Future Prospects: Looking ahead, the field of welding operator electronics is poised for further innovation and growth. Emerging technologies such as artificial intelligence, machine learning, and Internet of Things (IoT) connectivity promise to revolutionize welding processes by enabling predictive maintenance, autonomous welding systems, and real-time quality control.
Furthermore, advancements in materials science and additive manufacturing techniques are expanding the possibilities for welding operator electronics, opening up new opportunities for welding dissimilar materials, lightweight structures, and complex geometries.
Conclusion: Welding operator electronics have come a long way since their inception, transforming the welding industry and raising the bar for precision, efficiency, and quality. With continued innovation and integration of cutting-edge technologies, welding operators can look forward to enhanced capabilities and greater productivity in the years to come. As industries evolve and demand for high-performance welding solutions grows, welding operator electronics will remain at the forefront of technological advancement, driving progress and shaping the future of welding.