Welder (GTAW)
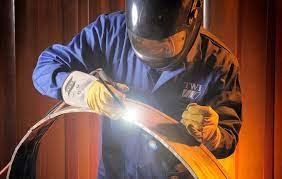
Introduction
Welding, often regarded as the cornerstone of modern fabrication, encompasses a diverse range of techniques, each with its own set of applications and intricacies. Among these techniques, Gas Tungsten Arc Welding (GTAW), also known as Tungsten Inert Gas (TIG) welding, stands out as a precise and versatile method prized for its ability to produce high-quality welds across various materials. In this article, we delve into the world of GTAW welding, exploring its principles, applications, techniques, and the skills required to master this art form.
Understanding GTAW Welding
GTAW welding employs a non-consumable tungsten electrode to create an arc between the electrode and the workpiece. The electrode, typically made of pure tungsten or a tungsten alloy, remains intact during the welding process, unlike consumable electrodes used in techniques like Shielded Metal Arc Welding (SMAW) or Gas Metal Arc Welding (GMAW).
A shielding gas, commonly argon or helium, is used to protect the weld area from atmospheric contamination, hence the term “inert gas” in TIG welding. This inert gas shield prevents oxidation and ensures a clean, high-quality weld bead.
The welding arc generated in GTAW is highly stable and controllable, making it suitable for welding thin materials and intricate joints. Additionally, GTAW allows for precise heat input control, minimizing distortion and heat-affected zone (HAZ) compared to other welding processes.
Applications of GTAW Welding
GTAW welding finds widespread use across numerous industries due to its versatility and ability to produce clean, aesthetically pleasing welds. Some common applications include:
- Aerospace: GTAW is extensively utilized in aerospace manufacturing for joining thin sheets of aluminum, titanium, and stainless steel with high precision and minimal distortion.
- Automotive: From fabricating exhaust systems to welding aluminum components in high-performance vehicles, GTAW plays a vital role in automotive manufacturing and repair.
- Pipelines: GTAW welding is employed in the construction and maintenance of pipelines for oil, gas, and water transportation, ensuring strong, leak-free joints.
- Stainless Steel Fabrication: The ability of GTAW to weld stainless steel with minimal distortion and excellent corrosion resistance makes it indispensable in industries such as food processing, pharmaceuticals, and architecture.
- Precision Instrumentation: GTAW is ideal for welding delicate components in precision instruments, electronic devices, and medical equipment, where weld quality and aesthetics are paramount.
Techniques and Equipment
Achieving mastery in GTAW welding requires proficiency in various techniques and familiarity with specialized equipment. Key aspects include:
- Electrode Selection: Tungsten electrodes come in different compositions, including pure tungsten, thoriated, ceriated, lanthanated, and zirconiated. The choice of electrode depends on factors such as material type, welding current, and desired arc characteristics.
- Shielding Gas: Selecting the appropriate shielding gas and flow rate is crucial to ensure adequate protection and weld quality. Argon is the most commonly used shielding gas due to its inertness and availability.
- Torch Setup: GTAW torches feature a precise control mechanism for adjusting welding current, gas flow, and electrode extension. Proper torch setup and manipulation are essential for maintaining arc stability and achieving desired weld penetration and profile.
- Welding Technique: GTAW offers various welding techniques, including freehand, weave, and orbital welding. Each technique has its advantages and is chosen based on joint geometry, material thickness, and weld specifications.
- Joint Preparation: Proper joint preparation, including cleaning, bevelling, and fit-up, is critical for achieving strong, defect-free welds. Careful attention to joint geometry and alignment minimizes the risk of weld discontinuities.
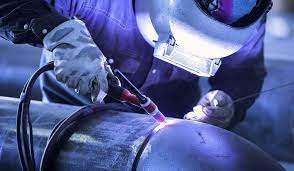
Skills and Training
Becoming proficient in GTAW welding requires a combination of theoretical knowledge, hands-on practice, and experience. Some essential skills and training considerations include:
- Understanding Welding Principles: A solid grasp of welding fundamentals, metallurgy, and heat transfer principles lays the foundation for successful GTAW welding.
- Hands-on Practice: Regular practice under the guidance of experienced instructors helps develop muscle memory, hand-eye coordination, and welding technique refinement.
- Safety Awareness: GTAW welding involves working with high temperatures, electrical currents, and potentially hazardous fumes. Prioritizing safety practices, including proper ventilation, personal protective equipment (PPE), and equipment maintenance, is imperative.
- Continual Learning: Keeping abreast of advancements in welding technology, materials, and techniques through workshops, seminars, and industry publications enhances welding skills and ensures adaptability to evolving requirements.
Conclusion
Gas Tungsten Arc Welding (GTAW) stands as a testament to the fusion of art and science in the realm of fabrication. Its precision, versatility, and ability to produce high-quality welds make it a preferred choice across diverse industries. Mastering GTAW welding requires dedication, practice, and a deep understanding of welding principles. As welding continues to evolve, GTAW remains a cornerstone technique, embodying the craftsmanship and skill essential for fabricating the world around us.