Quality Manager – Electronics
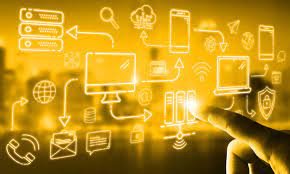
Introduction: In the intricate world of electronics manufacturing, ensuring quality is paramount. From consumer electronics to industrial equipment, the demand for flawless products is ever-growing. Amidst this demand, the role of a Quality Manager becomes indispensable. A Quality Manager in the electronics sector holds the responsibility of upholding stringent standards, ensuring product reliability, and maintaining customer satisfaction. In this article, we delve into the vital role of a Quality Manager in electronics manufacturing, exploring their responsibilities, challenges, and the strategies they employ to ensure excellence.
Responsibilities of a Quality Manager: The primary responsibility of a Quality Manager in the electronics industry revolves around maintaining and improving product quality throughout the manufacturing process. This encompasses various tasks:
- Quality Control Procedures: Developing, implementing, and maintaining quality control procedures is at the core of a Quality Manager’s role. This involves establishing quality benchmarks, conducting inspections, and implementing corrective measures to rectify any deviations from standards.
- Compliance Management: Ensuring compliance with industry regulations and standards is crucial for electronics manufacturers. Quality Managers must stay abreast of evolving regulatory requirements and oversee adherence to standards such as ISO 9001, IPC-A-610, and RoHS (Restriction of Hazardous Substances).
- Supplier Quality Management: Collaborating with suppliers to maintain the quality of incoming materials and components is essential for product reliability. Quality Managers establish stringent supplier evaluation processes and work closely with vendors to address any quality issues promptly.
- Process Improvement Initiatives: Continuous improvement lies at the heart of quality management. Quality Managers lead initiatives to optimize manufacturing processes, enhance efficiency, and minimize defects through methodologies like Six Sigma, Lean Manufacturing, and Total Quality Management (TQM).
- Customer Feedback Analysis: Gathering and analyzing customer feedback is vital for identifying areas of improvement and addressing customer concerns. Quality Managers utilize feedback mechanisms to enhance product quality and meet customer expectations.
Challenges Faced by Quality Managers: Quality Managers in the electronics sector encounter various challenges in their quest to maintain impeccable standards:
- Rapid Technological Advancements: The electronics industry is characterized by rapid technological advancements and shorter product lifecycles. Keeping pace with evolving technologies while ensuring quality can be daunting for Quality Managers.
- Supply Chain Complexity: Electronics manufacturing often involves complex global supply chains, increasing the risk of quality issues arising from disparate suppliers and logistics challenges. Managing quality across the supply chain poses a significant challenge for Quality Managers.
- Cost Pressures: Balancing quality objectives with cost constraints is a perpetual challenge faced by Quality Managers. The pressure to reduce manufacturing costs while maintaining high-quality standards requires strategic decision-making and efficient resource allocation.
- Regulatory Compliance: Compliance with stringent regulatory requirements adds another layer of complexity to quality management in the electronics industry. Quality Managers must navigate complex regulatory landscapes and ensure adherence to diverse standards across different markets.
Strategies for Ensuring Quality Excellence: To overcome these challenges and uphold superior quality standards, Quality Managers employ various strategies:
- Advanced Quality Control Technologies: Leveraging advanced technologies such as automated inspection systems, artificial intelligence (AI), and machine learning algorithms enhances the accuracy and efficiency of quality control processes, enabling early detection of defects.
- Collaborative Supplier Relationships: Building collaborative relationships with suppliers fosters transparency, accountability, and mutual support in maintaining quality standards. Quality Managers work closely with suppliers to establish clear quality criteria and foster continuous improvement initiatives.
- Cross-Functional Collaboration: Quality management is a cross-functional endeavor involving collaboration across departments such as R&D, manufacturing, procurement, and customer service. Quality Managers facilitate communication and collaboration among diverse teams to align quality objectives with overall business goals.
- Data-Driven Decision Making: Harnessing data analytics and quality metrics enables informed decision-making and proactive problem-solving. Quality Managers leverage data insights to identify trends, root causes of defects, and areas for process improvement, driving continuous quality enhancement.
- Employee Training and Empowerment: Investing in employee training and empowerment is critical for fostering a culture of quality excellence. Quality Managers provide comprehensive training programs, empower employees to take ownership of quality processes, and recognize and reward excellence to drive continuous improvement.
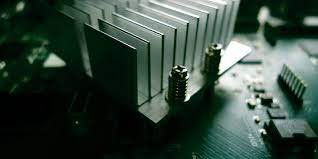
Conclusion: In the dynamic landscape of electronics manufacturing, the role of a Quality Manager is indispensable in ensuring product excellence, regulatory compliance, and customer satisfaction. Despite facing challenges such as rapid technological advancements, supply chain complexity, and cost pressures, Quality Managers employ proactive strategies to maintain impeccable quality standards. By embracing advanced technologies, fostering collaborative supplier relationships, promoting cross-functional collaboration, leveraging data-driven decision-making, and prioritizing employee training and empowerment, Quality Managers uphold the highest standards of quality excellence in the electronics industry.