Operator – Fluid Controls
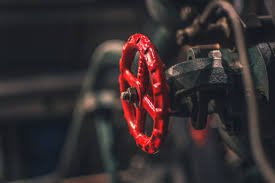
Introduction:
In the realm of mechanical engineering and industrial operations, efficient fluid control is paramount. Whether it’s managing the flow of liquids, gases, or other substances, precise control mechanisms are essential. This is where operator-fluid controls come into play, serving as the interface between operators and the complex systems they manage. In this comprehensive guide, we’ll delve into the intricacies of operator-fluid controls, exploring their functions, types, applications, and the latest advancements in the field.
Understanding Operator-Fluid Controls:
Operator-fluid controls, also known simply as control valves, act as the regulators of fluid flow within a system. These devices modulate the flow rate, pressure, temperature, and other parameters of the fluid to maintain optimal operation. They play a crucial role in a wide range of industries including oil and gas, chemical processing, water treatment, power generation, and many others.
Functionality of Operator-Fluid Controls:
The primary function of operator-fluid controls is to manage the flow of fluids within a system. They achieve this by precisely adjusting the size of the flow passage, thereby controlling the rate and direction of fluid flow. This regulation is typically achieved through various mechanisms such as throttling, on-off control, and pressure regulation.
Types of Operator-Fluid Controls:
Operator-fluid controls come in a variety of types, each designed to suit specific applications and operational requirements. Some common types include:
- Globe Valves: These valves feature a spherical body with an internal baffle and a movable plug (or disc) that regulates flow. They are commonly used for precise flow control in applications requiring moderate to high pressure differentials.
- Butterfly Valves: Butterfly valves employ a rotating disc to regulate flow within a pipe. They are lightweight, cost-effective, and suitable for applications requiring quick shut-off and minimal pressure drop.
- Ball Valves: Ball valves use a spherical closure unit (the ball) to control flow. They offer fast operation and tight sealing, making them ideal for on-off applications in industries such as petrochemicals and pharmaceuticals.
- Diaphragm Valves: Diaphragm valves utilize a flexible diaphragm to regulate flow. They are particularly well-suited for applications involving corrosive or abrasive fluids due to their excellent sealing capabilities.
- Control Valves: Control valves incorporate sophisticated actuators and control systems to precisely modulate fluid flow based on input signals. They are extensively used in automated processes where precise control is critical.
Applications of Operator-Fluid Controls:
The versatility of operator-fluid controls makes them indispensable across various industries. Some common applications include:
- Oil and Gas: Control valves are used in oil refineries, petrochemical plants, and natural gas processing facilities to regulate the flow of crude oil, refined products, and gases.
- Chemical Processing: In chemical plants, control valves play a vital role in controlling the flow of various chemicals and solvents throughout the production process.
- Water Treatment: Operator-fluid controls are utilized in water treatment plants to regulate the flow of water, chemicals, and additives for purification and distribution.
- Power Generation: Control valves are integral to power generation processes, where they control the flow of steam, water, and gases in boilers, turbines, and other equipment.
- HVAC Systems: In heating, ventilation, and air conditioning (HVAC) systems, control valves regulate the flow of water and air to maintain desired temperatures and comfort levels.
Advancements in Operator-Fluid Controls:
Recent advancements in technology have led to significant improvements in the design and performance of operator-fluid controls. Some notable advancements include:
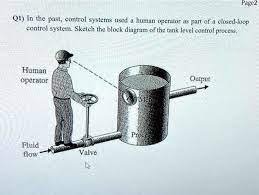
- Smart Valve Technology: Incorporation of sensors, actuators, and communication protocols enables control valves to gather real-time data, adjust parameters dynamically, and communicate with control systems for enhanced efficiency and reliability.
- Computational Fluid Dynamics (CFD) Analysis: Advanced computational techniques allow for detailed simulation and optimization of fluid flow within control valves, leading to improved designs with better performance and reduced energy consumption.
- Remote Monitoring and Control: Integration of IoT (Internet of Things) capabilities enables remote monitoring and control of control valves, allowing operators to manage systems from anywhere, optimize performance, and identify potential issues before they escalate.
- Enhanced Materials and Coatings: Development of new materials and coatings with superior corrosion resistance, wear resistance, and longevity enhances the durability and reliability of control valves, especially in harsh operating environments.
Conclusion:
Operator-fluid controls play a crucial role in ensuring the efficient operation of fluid systems across various industries. With advancements in technology and design, these devices continue to evolve, offering greater precision, reliability, and efficiency. By understanding the functions, types, applications, and advancements in operator-fluid controls, engineers and operators can make informed decisions to optimize fluid processes and enhance overall system performance.