Laser Marking & Cutting Process Engineer
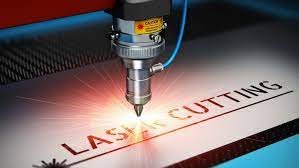
In the realm of modern manufacturing and engineering, precision is paramount. From intricate designs etched onto surfaces to the exacting cuts of materials, industries demand accuracy and efficiency. Laser technology has emerged as a stalwart in meeting these demands, offering versatile solutions for marking and cutting a plethora of materials with unparalleled precision. At the heart of harnessing this technology lies the Laser Marking & Cutting Process Engineer, a key figure driving innovation and efficiency in various sectors.
Understanding Laser Marking and Cutting
Before delving into the role of a Laser Marking & Cutting Process Engineer, it’s essential to grasp the fundamentals of laser marking and cutting processes. Laser marking involves using a high-energy laser beam to alter the surface of a material, creating marks, patterns, or designs without compromising the integrity of the substrate. This process finds applications in product branding, part identification, and aesthetic customization.
On the other hand, laser cutting utilizes a focused laser beam to precisely cut through materials, ranging from metals and plastics to fabrics and ceramics. The intense heat generated by the laser vaporizes or melts the material along the desired cutting path, producing clean and accurate edges. Industries such as automotive, aerospace, electronics, and fashion rely on laser cutting for prototyping, mass production, and intricate designs.
The Role of a Laser Marking & Cutting Process Engineer
A Laser Marking & Cutting Process Engineer is a multifaceted professional responsible for optimizing laser-based manufacturing processes to achieve superior quality, efficiency, and cost-effectiveness. Their role encompasses a spectrum of tasks, including design optimization, process development, equipment maintenance, and quality assurance. Let’s explore the core responsibilities in detail:
- Process Optimization: Engineers analyze the intricacies of materials and laser systems to optimize marking and cutting parameters. This involves determining the appropriate laser power, wavelength, pulse duration, and scanning speed to achieve desired results while minimizing thermal damage or distortion.
- Equipment Selection and Integration: Selecting the right laser equipment is crucial for achieving desired outcomes. Process engineers evaluate available laser technologies and work closely with equipment suppliers to integrate suitable systems into manufacturing setups. They ensure seamless compatibility and performance consistency across various production lines.
- Design for Manufacturing (DFM): Collaborating with design teams, process engineers provide valuable input on designing products for efficient laser processing. They optimize designs for manufacturability, considering factors such as material compatibility, feature size, and geometric complexity. DFM principles help streamline production workflows and minimize post-processing requirements.
- Quality Control and Assurance: Maintaining stringent quality standards is imperative in laser-based manufacturing. Engineers develop and implement robust quality control protocols to inspect marked or cut components for accuracy, consistency, and adherence to specifications. They leverage advanced metrology techniques and automated inspection systems to ensure product integrity and customer satisfaction.
- Process Monitoring and Maintenance: Continuous monitoring of laser processes is essential for preempting potential issues and ensuring uninterrupted production. Engineers deploy sensor systems and data analytics tools to monitor key process parameters in real-time, facilitating proactive maintenance and troubleshooting. Regular maintenance routines are established to uphold equipment performance and prolong service life.
- Regulatory Compliance and Safety: Laser technologies are subject to stringent regulatory requirements and safety standards. Process engineers stay abreast of industry regulations and implement safety protocols to mitigate risks associated with laser operation. They conduct thorough risk assessments, provide training to personnel, and maintain compliance with applicable standards such as ANSI Z136 and FDA regulations.
- Research and Innovation: As pioneers in laser technology, process engineers engage in continuous research and innovation to push the boundaries of what’s possible. They explore novel materials, laser sources, and processing techniques to expand the application scope and enhance productivity. Collaborations with academic institutions and industry partners foster breakthroughs in laser processing capabilities.
Challenges and Future Directions
While laser technology offers unparalleled precision and versatility, Laser Marking & Cutting Process Engineers encounter several challenges in their pursuit of excellence. These include optimizing process speed without compromising quality, overcoming material-specific limitations, and integrating complex automation solutions for high-volume production.
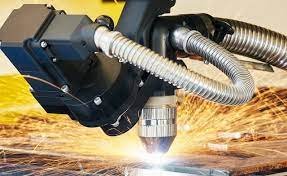
Looking ahead, the field of laser-based manufacturing is poised for significant advancements driven by emerging technologies such as ultrafast lasers, additive manufacturing, and artificial intelligence. Laser Marking & Cutting Process Engineers will play a pivotal role in harnessing these innovations to unlock new possibilities in industries ranging from medical devices and consumer electronics to renewable energy and beyond.
Conclusion
In the ever-evolving landscape of modern manufacturing, Laser Marking & Cutting Process Engineers stand as architects of precision, leveraging laser technology to redefine the boundaries of possibility. Their expertise in optimizing processes, ensuring quality, and driving innovation enables industries to achieve new heights of efficiency and product excellence. As the demand for precision manufacturing continues to soar, the role of these engineers will remain indispensable in shaping the future of industrial production.