Assistant – Machinist – Iron And Steel
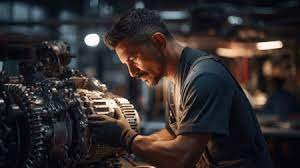
Introduction
In the dynamic landscape of the iron and steel industry, where precision and efficiency are paramount, the integration of Artificial Intelligence (AI) has revolutionized traditional machinist workflows. AI assistants have emerged as invaluable tools, augmenting human expertise with advanced analytics, predictive capabilities, and automation. This article explores the role of AI assistants in the context of machinist operations within the iron and steel sector, highlighting their impact on productivity, quality assurance, and innovation.
The Evolution of Machinist Workflows
Machinists play a crucial role in the iron and steel industry, tasked with shaping raw materials into precision components using various machining techniques. Traditionally, machinist workflows relied heavily on manual processes, involving meticulous measurements, trial-and-error adjustments, and extensive human intervention. While these methods have yielded satisfactory results, they are often time-consuming, labor-intensive, and prone to errors.
With advancements in technology, particularly in AI and machine learning, the landscape of machinist workflows has undergone a significant transformation. AI-powered assistants have emerged as intelligent counterparts to human machinists, offering a range of capabilities aimed at streamlining operations and optimizing outcomes.
Enhancing Precision and Accuracy
One of the primary advantages of AI assistants in machinist workflows is their ability to enhance precision and accuracy. Through advanced algorithms and data analysis, these assistants can identify subtle variations in material properties, tool performance, and machining parameters. By continuously monitoring and adjusting these variables in real-time, AI assistants ensure consistent quality and dimensional accuracy in the manufactured components.
For instance, in the milling process, AI assistants can analyze tool wear patterns, predict potential deviations, and optimize cutting parameters to maintain precise tolerances. Similarly, in turning operations, AI can adjust spindle speeds, feed rates, and tool paths based on dynamic feedback, resulting in smoother surface finishes and reduced scrap rates.
Predictive Maintenance and Optimization
AI assistants also play a crucial role in predictive maintenance, a proactive approach to equipment upkeep aimed at minimizing downtime and maximizing productivity. By analyzing sensor data from machining equipment, AI algorithms can anticipate potential failures or performance degradation before they occur.
In the context of iron and steel machining, where heavy-duty equipment is subjected to extreme operating conditions, predictive maintenance can prevent costly breakdowns and production delays. AI assistants can monitor factors such as temperature, vibration, and lubrication levels, flagging any anomalies that may indicate impending issues. Machinists can then take preemptive measures, such as scheduling maintenance tasks or replacing worn components, during planned downtime periods, minimizing disruptions to production schedules.
Furthermore, AI-powered optimization algorithms can fine-tune machining parameters to maximize efficiency while minimizing energy consumption and material waste. By analyzing historical data and real-time performance metrics, AI assistants can identify optimal cutting speeds, tool paths, and coolant usage strategies, resulting in significant cost savings and environmental benefits.
Streamlining Workflow Management
Another area where AI assistants excel is in streamlining workflow management and resource allocation. By analyzing production schedules, material availability, and machine capacities, AI algorithms can optimize job prioritization and scheduling, ensuring optimal utilization of resources and minimizing idle time.
For example, when faced with a sudden rush order or unexpected equipment downtime, AI assistants can automatically reconfigure production schedules, reallocating tasks to available machines or adjusting shift assignments to meet deadlines. Additionally, AI-powered inventory management systems can anticipate material requirements based on projected demand, optimizing stocking levels and minimizing the risk of stockouts or overages.
Quality Assurance and Defect Detection
Quality assurance is of paramount importance in the iron and steel industry, where even minor defects can compromise the structural integrity and performance of manufactured components. AI assistants play a crucial role in quality control by leveraging advanced imaging techniques, such as computer vision, to inspect finished parts for defects, surface irregularities, or dimensional deviations.
Using machine learning algorithms trained on vast datasets of annotated images, AI assistants can quickly identify anomalies that may escape human detection, such as microcracks, surface pitting, or incomplete welds. By flagging these issues in real-time, machinists can take corrective action immediately, preventing defective parts from entering the supply chain and ensuring compliance with stringent quality standards.
Furthermore, AI-powered defect detection systems can provide valuable insights into root causes and process improvements, helping machinists identify underlying issues, such as tool wear, machine misalignment, or material impurities, that may contribute to defects. By addressing these issues proactively, manufacturers can continuously enhance process reliability and product quality, fostering customer satisfaction and brand reputation.
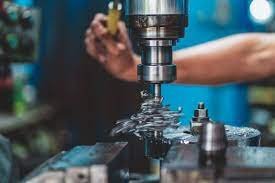
Collaborative Human-AI Workflows
It’s essential to note that AI assistants are not intended to replace human machinists but rather to complement their expertise and augment their capabilities. The most effective workflows in the iron and steel industry involve close collaboration between human operators and AI systems, leveraging the strengths of each to achieve optimal outcomes.
Human machinists bring domain expertise, problem-solving skills, and creativity to the table, while AI assistants provide data-driven insights, predictive capabilities, and automation capabilities. By working together seamlessly, machinists and AI systems can tackle complex challenges, adapt to changing conditions, and drive continuous improvement in manufacturing processes.
Conclusion
In conclusion, AI assistants have emerged as indispensable tools in modern machinist workflows within the iron and steel industry, offering a range of capabilities aimed at enhancing precision, productivity, and quality assurance. By leveraging advanced algorithms, predictive analytics, and automation technologies, AI assistants empower machinists to optimize processes, minimize downtime, and deliver superior products to market. As technology continues to evolve, the symbiotic relationship between human expertise and AI-driven innovation will undoubtedly shape the future of machining in the iron and steel sector, driving efficiency, sustainability, and competitiveness in an ever-changing landscape.