Wiring Harness Assembly Operator
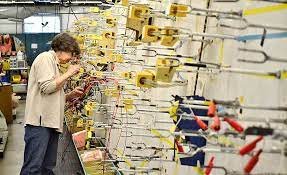
In the intricate world of modern manufacturing, where precision and efficiency reign supreme, every component plays a vital role in the final product’s functionality and quality. Among these crucial components, wiring harnesses stand as the intricate nerve systems, facilitating the seamless flow of electrical power and signals within various devices and machinery. At the heart of the production process lies the Wiring Harness Assembly Operator, a skilled individual tasked with the meticulous assembly of these complex networks. In this article, we delve into the role of Wiring Harness Assembly Operators, exploring their responsibilities, skills, and significance within the manufacturing landscape.
Understanding Wiring Harness Assembly
Before delving into the specifics of the Wiring Harness Assembly Operator’s role, it’s essential to grasp the fundamentals of wiring harnesses. A wiring harness is a comprehensive assembly of wires, connectors, terminals, and other components, meticulously arranged to transmit power and signals efficiently within a device or system. These harnesses vary greatly in complexity, ranging from simple configurations in household appliances to intricate networks found in automotive and aerospace applications.
The Role of Wiring Harness Assembly Operators
Wiring Harness Assembly Operators are integral to the manufacturing process, as they are responsible for the precise assembly of these complex electrical systems. Their role encompasses a range of tasks, each requiring precision, attention to detail, and technical expertise.
- Interpreting Blueprints and Specifications: One of the primary responsibilities of Wiring Harness Assembly Operators is to interpret technical drawings, blueprints, and specifications provided by engineers. These documents outline the exact configuration and layout of the wiring harness, including the types of wires, connectors, and terminals to be used.
- Cutting and Stripping Wires: With the blueprint as a guide, operators must accurately measure, cut, and strip the wires to the required lengths. This process demands precision to ensure that each wire is cut to the correct dimensions and stripped of insulation without damaging the conductive core.
- Crimping and Terminating: Once the wires are prepared, the next step involves crimping connectors and terminals onto the ends of the wires. Wiring Harness Assembly Operators utilize specialized tools and equipment to perform these tasks, ensuring a secure and reliable connection that can withstand the rigors of operation.
- Routing and Lacing: With the individual wires prepared and terminated, operators proceed to route and bundle them according to the blueprint’s specifications. This step requires careful attention to detail to prevent tangling or crossing of wires, which could lead to electrical faults or malfunction.
- Testing and Quality Control: Before the completed wiring harness is integrated into the final product, it undergoes rigorous testing to ensure functionality and reliability. Wiring Harness Assembly Operators may perform continuity tests, insulation resistance tests, and other quality control checks to verify the integrity of the assembly.
- Adhering to Safety Standards: Throughout the assembly process, Wiring Harness Assembly Operators must adhere to strict safety protocols to mitigate the risk of electrical hazards and ensure the well-being of themselves and their colleagues. This includes proper handling of tools and equipment, wearing appropriate personal protective equipment, and following established procedures for handling hazardous materials.
Skills and Qualifications
Becoming a proficient Wiring Harness Assembly Operator requires a combination of technical skills, practical experience, and attention to detail. While specific requirements may vary depending on the employer and industry, the following skills and qualifications are typically sought after:
- Technical Aptitude: A solid understanding of electrical principles, wiring techniques, and assembly processes is essential for success in this role. Wiring Harness Assembly Operators must be able to interpret technical drawings, use specialized tools and equipment, and troubleshoot electrical issues as they arise.
- Manual Dexterity: The assembly of wiring harnesses often involves working with small components and intricate connections. As such, strong hand-eye coordination and manual dexterity are essential for performing tasks such as crimping, soldering, and routing wires with precision.
- Attention to Detail: The devil is in the details when it comes to wiring harness assembly. Operators must pay close attention to the specifications outlined in the blueprints, ensuring that each wire is cut, stripped, and terminated correctly to prevent any errors or defects in the final assembly.
- Problem-Solving Skills: Despite careful planning and preparation, challenges and obstacles may arise during the assembly process. Wiring Harness Assembly Operators must possess strong problem-solving skills to identify issues, implement effective solutions, and ensure that production deadlines are met without compromising quality.
- Teamwork and Communication: Collaboration is often a key aspect of manufacturing environments, and Wiring Harness Assembly Operators must be able to work effectively as part of a team. Clear communication with colleagues, supervisors, and engineers is essential for coordinating tasks, sharing information, and resolving any issues that may arise during the assembly process.
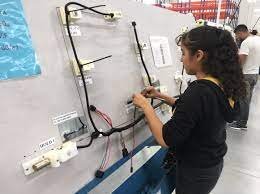
Conclusion
In the intricate tapestry of modern manufacturing, Wiring Harness Assembly Operators stand as unsung heroes, meticulously crafting the intricate nerve systems that power our devices and machinery. Through their expertise, precision, and dedication, they ensure that each wiring harness meets the highest standards of quality, reliability, and performance. As technology continues to advance and demand for electrical systems grows, the role of Wiring Harness Assembly Operators will remain indispensable, driving innovation and progress across a myriad of industries.